Windows and doors
- ramshawmartin
- Aug 11, 2019
- 2 min read
Since the roof went up, our house has been wrapped in unsightly polythene to prevent rain blowing in through the door and window openings. The first week in August was a major milestone for us - installation of our Internorm glazing by a team from Ecohaus.
Before and after ..


Gary and his team of 3 fitters arrived from Stroud, shortly followed by our glass on the back of an open lorry. The triple glazed units were very heavy but were lifted off using a crane and suckers.



A robotically controlled sucker machine was used to lift the large glazed units into position with millimetre tolerances. There was an instantaneous change in the feel of the house as the structure was now complete.
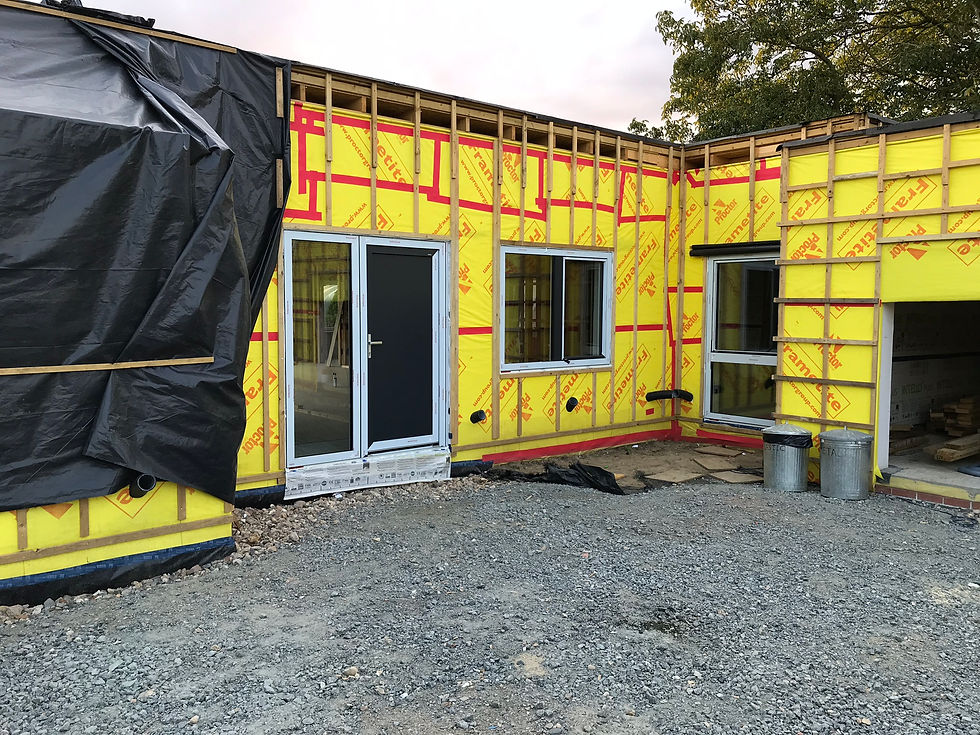
We have a full height sliding door in the south wall that will open on to a deck and the garden - it worked perfectly first time.
Our other windows and doors are uPVC frames with aluminium trim outside. Gary and his team took great care to seal and finish them to a high standard.
Our groundworkers (James and Tim from Norfolk Property Services) also returned to dig the service trenches around the back of the house.
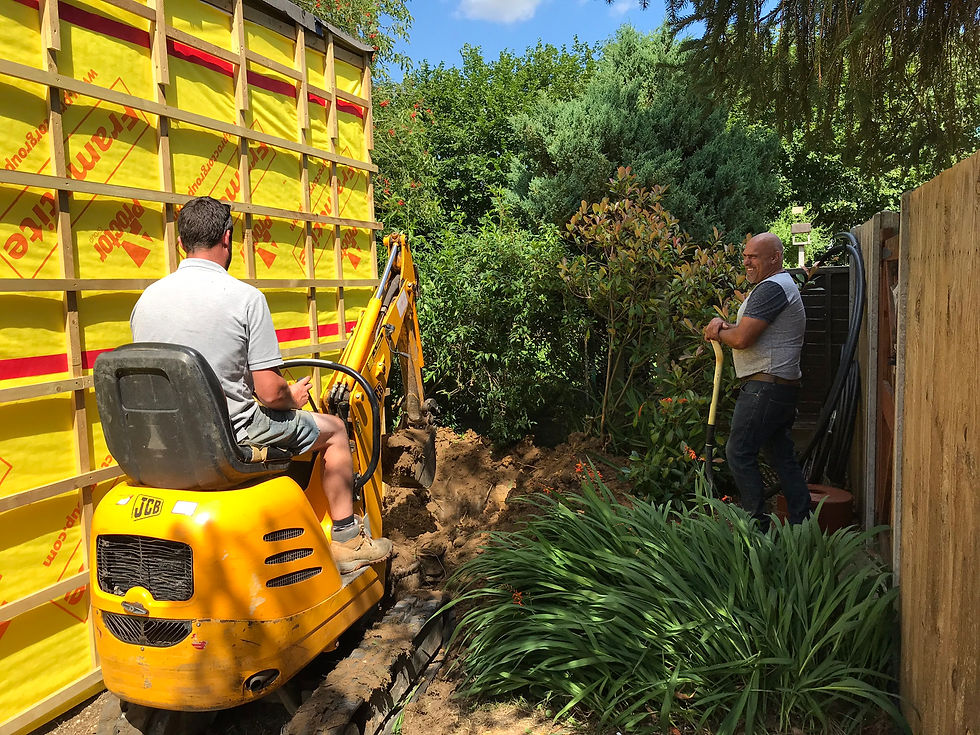


We have 2 water supply pipes - the standard 32mm water main and a 50mm supply for the fire sprinkler system we are installing. This needs a ridiculously large stop valve in the utility room.
Sarah and I have built all of the internal walls, revealing the layout of the rooms - we are now expert in studs and noggins. We also built a pocket for a sliding bathroom door.


With Beattie finished, next was the air tightness test. The Passivhaus standard requires a maximum of 0.6 air changes per hour.

To perform the test, a fan unit sealed into the front door opening was used to pressurise the building to 50 Pa above atmospheric pressure. The fan was then reversed to lower the pressure by the same amount. The pressure inside was monitored and we also checks for obvious leaks e.g. around the doors and windows.
We passed with flying colours - a reading of 0.3. This has given us a lot of confidence in the Beattie system and their attention to detail on the taping.

The house was then heated to 45 degrees Celsius and the internal surfaces scanned with an IR camera to identify any cold spots that would indicate unwanted thermal bridges.
All the internal surfaces (including the glass) were within a few degrees of the same temperature.
Our house has become a home.
Comments